Comparison of Gel Extrusion Technologies: Piston, Air and Screws, for the Manufacture of Personalized Medicines
in a pharmaceutical sector in constant evolution, pharmaceutical 3D printing makes it possible to visualize a new way to produce personalized medicines on demand. Several 3D printing technologies exist on the market. Among these techniques, 3D printing from pharmaceutical gels is particularly promising in the new era of personalized medicine. The gel extrusion 3D printing process relies on an uninterrupted flow of material delivered from a cartridge. This method has various advantages, including the ability to print a wide range of viscosities by adjusting pressure. It also allows the coextrusion of two separate gels. In addition, 3D printing of pharmaceutical gels operates at moderate temperatures. This technology is therefore ideal for temperature-sensitive components.
Several gel 3D printing technologies exist on the market. Each with their advantages and disadvantages, which is why we invite you to discover the three main ways to extrude pharmaceutical gels by 3D printing.
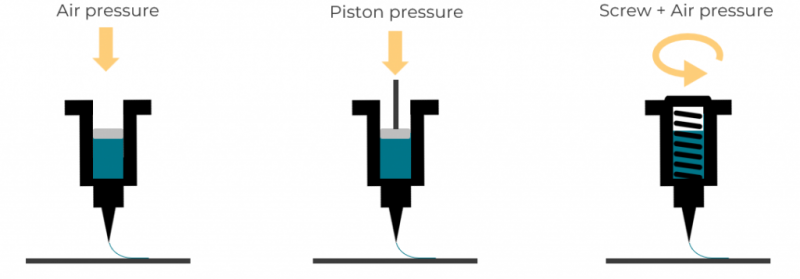
3D printing of gels by air pressure
Pharmaceutical 3D printing using air pressure is a technique widely adopted for its simplicity of execution. The application of air pressure pushes a piston into contact with the material into the syringe, facilitating its extrusion through a nozzle. This process makes it possible to deposit the material on a tray, thus promoting the manufacture of personalized and specific medicines.
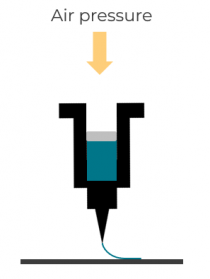
Air pressure gel extrusion diagram
This method may have delays in deposition due to compression of the gas contained in the cartridge. This will lead to a decrease in printing accuracy. In systems using air pressure, flow cannot be directly controlled. The flow rate depends on the pressure applied, the size of the nozzle and the environment.
This feature can lead to variations in flow. It is also important to note that environmental conditions can influence flow rate and induce filing inaccuracies. For example, temperature, humidity, as well as parameters related to cartridge filling and material properties, such as inhomogeneity or batch variations, can impact the quality of printed medicines. Careful consideration of parameters is essential to ensure successful 3D printing of pharmaceutical gels and personalized medicines.
3D printing of gels by mechanical pressure
Pharmaceutical 3D printing of gels, using mechanical pressure technique, enables the precise extrusion of pharmaceutical gels. This technology extrudes the gel thanks to the force exerted on a plunger in contact with the material contained in the dedicated syringe.
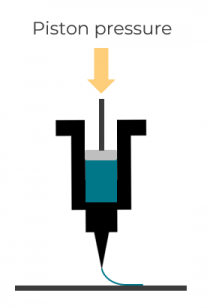
Diagram of gel extrusion by mechanical system
Mechanical pressure systems offer theoretically more accurate extruded volume control than air pressure 3D printing technologies. Indeed, by the movement of the piston in the pharmaceutical cartridge, it is possible to control the flow. Although the flow rate can be independently adjusted by adjusting the speed of the plunger, there may be delays due to the elasticity of the gels and variations due to the friction of the plunger on the syringe. Integrating a peristaltic pump on the extruder overcomes these problems, but creates increased complexity, additional costs, and additional challenges in terms of maintaining and cleaning the 3D print head. This 3D printing technique usually does not allow printing highly viscous materials. Indeed, there is a risk of material leakage through the piston during the application of high mechanical pressure. Nevertheless, this technology paves the way for the realization of personalized medicines through 3D printing.
3D printing of gels by volumetric dosing
3D printing of drugs by volumetric dosing works using an auger. The latter will transport the material to the output of the 3D printing head.
The 3D printing of pharmaceutical gels by volumetric dosing represents a significant advance in the manufacture of personalized medicines. This method involves careful control of the volume of gel-like material extruded at each layer. This ensures high precision in the creation of complex structures.
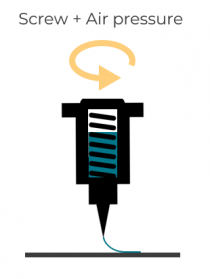
Volumetric dosing gel extrusion diagram
Unlike pharmaceutical 3D printing methods by mechanical pressure and air, where mechanical or pneumatic forces are used for extrusion. Volumetric dosing eliminates flow delays and variations due to friction. Volumetric dosing systems allow precise and independent adjustment of the flow rate depending on the material. These systems ensure better reproducibility and consistent quality of printed pharmaceutical products. Very viscous materials can be printed using this technology. In addition, this approach reduces the complexity and costs associated with integrating additional mechanical or pneumatic components. However, the dead volume in the duct can generate a small loss of material.
3D printing of pharmaceutical gels by volumetric dosing paves the way for more reliable, efficient and personalized drug production. While minimizing the technical challenges encountered with other extrusion methods. That’s why MB Therapeutics team chooses to integrate pharmaceutical 3D printing by volumetric dosing without cleaning needed between batches for the rapid formulation development. Allowing to benefit from the advantages of 3D printing technology by volumetric dosing without the disadvantages.
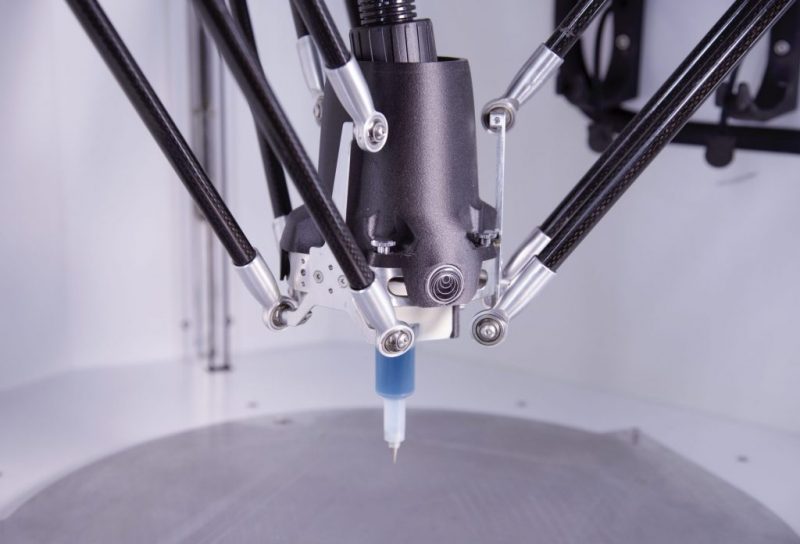
GEL technology integrated into the pharmaceutical 3D printer: MED-U Modular
Conclusion
In conclusion, the evolution of pharmaceutical 3D printing technology offers exciting prospects for the future of personalized medicine. Especially to improve the care of children. Among the various methods of extrusion of pharmaceutical gels, volumetric dosing stands out for its accuracy and potential to eliminate the challenges associated with flow delays and variations. This promising approach offers a reliable solution for the production of tailor-made medicines, while reducing technical complexity and costs. It is clear that 3D printing of pharmaceutical gels is one of the key options for providing quality care to children and patients of all ages. Paving the way for personalized medicine tailored to each individual’s unique needs.